Jornada Amazônia [Amazon Journey]
The Amazon Journey Program aims to design and implement a broad set of organizational actions, whose general objective is forest conservation through the establishment of an ecosystem of entrepreneurship and innovation of impact in the Amazon. It has the following premises: -The competitiveness of the standing forest can be fostered by innovation and entrepreneurship Innovative […]
Braille Modular Printer
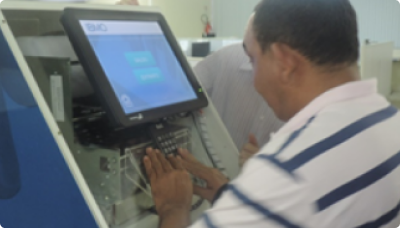
Client: Tecassistiva Financing: FINEP Equipped with robust hardware and a software architecture that will enable its integration with ATMs and other types of access terminals, the Braille Modular Printer (IBMO) is designed to print bank balances and statements in braille, enabling broader access for thousands of visually impaired people to automated services, providing this target […]
Education 4.0
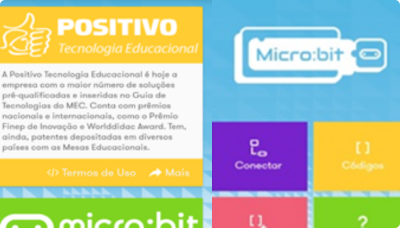
Client: Positivo Development of a set of innovative educational solutions that integrate with the micro:bit and LEGO Mindstorms platforms, with the goal of educating Brazilian children and youth in basic computing and computer programming concepts. Research and development of an Innovative Educational Solution for POSITIVO, which involved electronic, mechanical and software design and development to […]
PPE Monitoring Using Wearable Technology
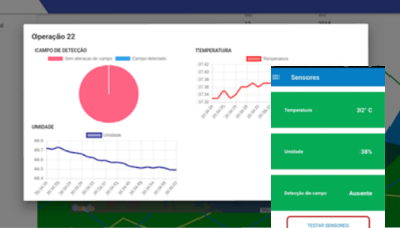
Client: Amazonas Distribuidora de Energia The project, contemplated through Public Call for R&D projects 2015/2016, consisted of developing an experimental version of clothing for fieldwork technicians at Amazonas Distribuidora de Energia. The main idea was to provide the PPE suit with intelligence to minimize workplace risks and accidents. An Android app was developed to initiate […]
Production and Quality Management System (PROMES)
Client: Proeletronic Development and implementation of the MES (Manufacturing Execution System) comprised of four main modules: Shop Floor Control: enables the collection and recording of information from assembly lines and the later generation of reports on production progress. Quality Management System: enables the recording of information related to assembly line inspection and quality processes and […]
ESD Inspection Management System
Client: Universal Eletronics Development of a web system, responsive to client-server type, which manages activities for combating ESD. The functions can be accessed with a browser on devices such as smartphones or tablets (Android OS), facilitating the recording of industrial inspections. The main functions of this system are: Registration and management of inspection activities Scheduling […]
Auditing management system (QMS)
Client: Inventus Power A system that allows automating parts of the auditing process: research and data correlation, storage of relevant records and documents, flagging, and monitoring actions inherent to the flow of decision-making. The QMS enables the creation of auditing flows, by applying parameters to the flow of the process to be audited, in which […]
An automated system for manufacturing machines (SIAMM)
Client: Positron A system for the automatic collection of operational information from the injection-molding machine facilities, capable of integrating both injectors equipped with native communication interfaces (serial or other protocols) and injectors without connectivity, in which the collection of electronic signals directly from the machine’s control panels was enabled. It has a monitoring software layer […]
Automation of the testing process for RFID chips
Client: SMARTRAC Electromechanical and software development for a machine capable of automatically testing and registering RFID inlays arranged in a matrix of up to 6 x 10, comprising: Process mapping and diagnostics Specification of alternative solutions Software, hardware, and mechanical development Performance and usability tests Integration, training, and operationalization